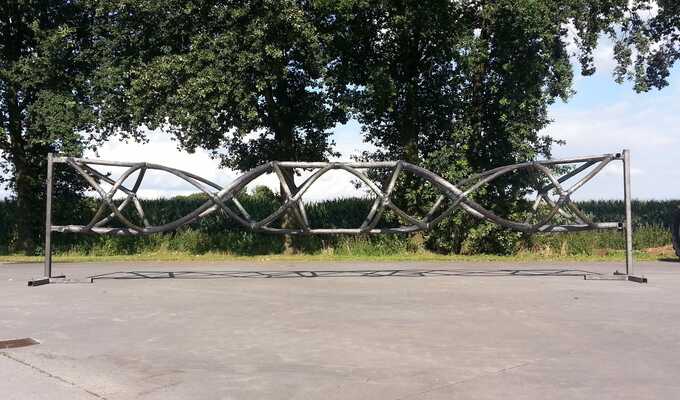
Thesis Rigidized Inflatables
Grades:
Presentation: 8
Proces: 8,5
Product: 8,5
This thesis describes the development of an innovative production method for structurally optimized section active structure systems. The research stems from the growing demand of society to reduce material use in the construction sector, in turn reducing resource depletion. An answer to this issue is found in the use of structural optimization to reduce the weight of structural elements. However, currently there are no efficient production methods which are suited for producing the organic shapes distinctive for structurally optimized elements. Due to its nature to conform to funicular shapes, a production method based on inflatable membranes which can be partly or fully rigidized is believed to be a promising solution. In that case the formwork of the three-dimensional structure consists entirely of inflatables and is therefore completely based on form-active principles. The method uses an inner inflatable, or secondary mould, which serves as falsework and is either temporary or semi-permanent. On the outer surface of the secondary mould, tubes which can be partly or fully rigidized are inflated and represent the optimized structural element.
The study started with an in depth literature review into the fundamentals of structural optimization. Subsequently, topology optimization by mean of empirical case studies was performed on the section active structure systems to determine their general morphological features. This showed that the relation between structure and form, i.e. the structural morphology, of these optimized elements is very strong. The resulting topology and morphology of an optimization routine is determined by the force distribution through the design space and the different constraints and performance requirements that act on that specific design space. Since the morphology of an optimized one-bay beam can be recognized in every optimized section active structure system, and most of the general morphological features are reflected in an optimized beam, it served as a case for the proposed production method. This topologically optimized three dimensional beam was then shape optimized using the ParaGen method. With this parametric method, a population of 1276 different solutions was created algorithmically. The solution with the highest specific stiffness was finally size optimized using STAADpro.
Literature reviews were also performed to determine the most suitable inflatable structure typology and envelope material for the secondary mould. This study revealed five typologies which were assessed according to four morphological indicators. The four optimized section active structure systems were assessed according to the same indicators in order to compare the inflatable typologies to the optimized structures. The resulting matrix showed that a straight high pressure system was the best inflatable typology to use as the secondary mould for our case. In addition, the literature review into envelope materials revealed the properties and characteristics of membrane materials in general. Moreover, it showed that, according to ten criteria relevant to this research, PVC coated polyester could best be used for the fabrication of the secondary mould.
The final step in the research phase included a literature review into rigidization method used for terrestrial and space applications. This study, together with feedback from several experts, showed that no single rigidizable material for space applications can be transferred to the construction industry directly. However, their main advantages, e.g. rigidization on command, can be utilized when combining their structure with commercial manufacturing methods such as resin transfer moulding or vacuum infusion.
The results of the research phase formed the foundation of the development phase, which started with a full structural analysis of the model based on detailed requirements and conditions in GSA and STAADpro. Parallel to this analysis, twelve concrete scale models were fabricated of four different geometries. These scale models showed that certain geometries were disadvantageous compared to their finite element model which used straight members. It also showed that the geometry that was chosen as the case indeed possessed the highest stiffness.
Together with the structural analysis, all the information needed for the fabrication of the prototype was known. The prototype was fabricated of braided glass fibre tubes which were inflated around an inflated PVC coated polyester tube. The glass fibre was finally impregnated with a polyester resin using hand lay-up, leaving the final rigidized optimized structure.
With the fabrication of the prototype the proposed production method was demonstrated in full scale. The main advantages of the method are its extremely low self weight and rapid deployability, which can be increased when a rigidization method use in space can be utilized. The system can either be kept inflated or can be rigidized to make the structure independent of air pressure, increasing the possible applications of the method. Rigidized inflatables can for example be used for emergency relief, temporary structures, military applications, or for the reinforcement of existing structures. The secondary mould can be removed to leave a rigid structural element, but research still has to be done into the combination of a rigid optimized outer structure and inflated inner tube. In this case, the entire structure will act as a tensairity. Here, the strength will be larger than the sum of the individual parts, rendering an extremely light weight, rapid deployable, high strength element.